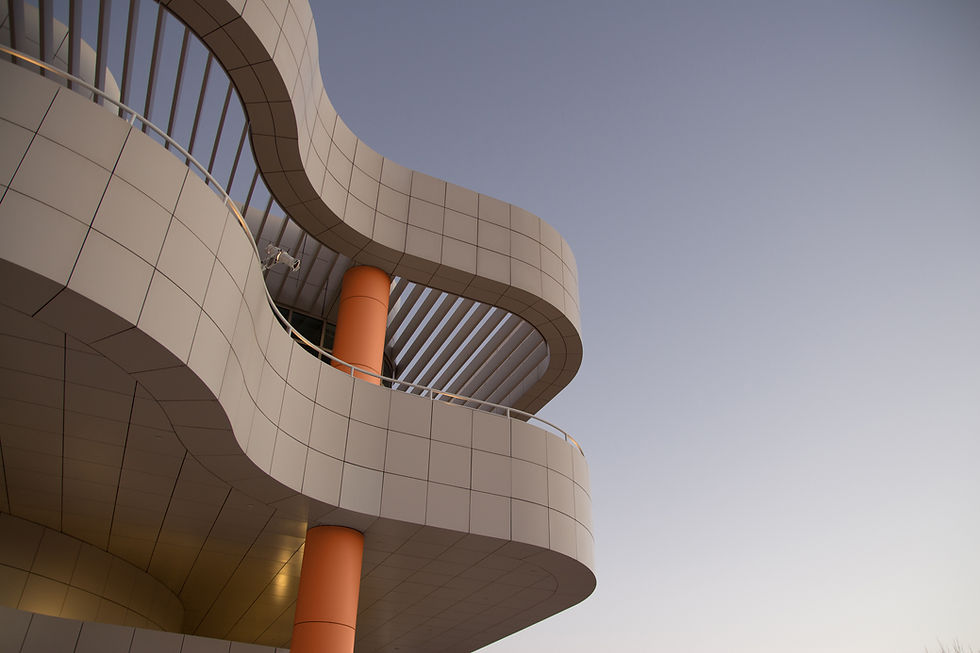
The Role of PCBs in the Automotive Industry: Driving Innovation and Reliability
1
7
0

In modern vehicles, technological advancements have transformed the automotive landscape, making them smarter, more efficient, and safer. At the core of many of these innovations is the Printed Circuit Board (PCB). Automotive PCBs serve as the foundation for numerous electronic systems within a vehicle, enabling features that range from infotainment to critical safety functions like anti-lock braking systems (ABS) and advanced driver-assistance systems (ADAS).
What Are Automotive PCBs?
PCBs are thin boards made of non-conductive materials, such as fiberglass, with conductive pathways etched or printed onto them to connect various electronic components. In the automotive industry, PCBs are essential for supporting and integrating the numerous electronics that control everything from basic operations, like engine control, to advanced systems like autonomous driving.
Automotive PCBs need to meet strict requirements due to the harsh conditions vehicles operate under. High temperatures, vibrations, humidity, and dust are common, so PCBs must be durable and reliable in extreme environments. Automotive-grade PCBs typically feature high-temperature laminates, heavy copper layers, and enhanced protection to ensure long-lasting performance.
Types of PCBs in Automotive Applications
Several types of PCBs are used in vehicles, each designed for specific functions:
Single-Sided PCBs: These are the simplest type, where the circuit is printed on one side of the board. They are often used in less complex systems, such as LED lighting or basic control units.
Double-Sided PCBs: These boards feature circuits on both sides, connected by vias (small holes). They are more versatile and are used in slightly more complex systems, such as engine control units (ECUs).
Multilayer PCBs: These contain multiple layers of circuits sandwiched together. Multilayer PCBs are essential in sophisticated systems such as ADAS, powertrain control, and autonomous driving technologies.
Flexible PCBs: These boards are designed to bend and conform to different shapes, making them ideal for compact or curved spaces within a vehicle, such as in dashboards or touch panels.
Rigid-Flex PCBs: A hybrid of rigid and flexible PCBs, these are used when components need to be mounted in hard-to-reach places without sacrificing the board’s integrity. They are commonly found in airbags and other safety-critical systems.
Applications of PCBs in Automotive Systems
PCBs are crucial in several automotive systems, and their role is only expanding as cars become more intelligent and interconnected. Here are some key applications:
Engine Control Units (ECUs): PCBs within ECUs process data from various sensors to control engine functions like fuel injection, ignition timing, and emissions control. As vehicles move toward electrification, PCBs in ECUs must manage even more complex tasks.
Infotainment Systems: Entertainment and navigation systems rely heavily on PCBs to process multimedia data, handle connectivity (Bluetooth, Wi-Fi), and control user interfaces. Flexible PCBs are commonly used in the compact spaces behind touchscreens and control panels.
Safety Systems: PCBs are at the heart of safety-critical systems such as ABS, airbag deployment, and ADAS. These boards must be extremely reliable, as they play a vital role in preventing accidents and protecting passengers.
Electric Vehicles (EVs): In electric and hybrid vehicles, PCBs manage high-power battery systems, regenerative braking, and energy distribution. The demand for durable PCBs is even greater in EVs due to the higher operating temperatures and power loads.
Lighting Systems: Automotive lighting, particularly LED headlights and interior lighting, relies on PCBs for power management and control. These boards help ensure energy efficiency and long-lasting performance.
Challenges in Automotive PCB Design
Designing PCBs for the automotive industry comes with unique challenges. The harsh operating environment of vehicles means that PCBs must meet stringent durability standards. Some of the primary challenges include:
Heat Management: Vehicles generate significant heat, especially in areas near the engine or power electronics in EVs. PCBs must be designed to dissipate heat efficiently, often requiring the use of heavy copper layers and thermal vias to prevent overheating.
Vibration and Shock: Automobiles experience constant vibrations and mechanical shocks. PCBs need to be robust and securely mounted to avoid connection failures, making material choice and component placement critical factors in design.
Environmental Resistance: Automotive PCBs are exposed to dust, moisture, and chemicals. Proper coatings and protective layers, such as conformal coatings, are required to protect the boards from environmental damage.
Complexity and Miniaturization: As vehicles become more advanced, the number of electronic components packed into a PCB increases. Designers face the challenge of miniaturizing components while ensuring that the board’s electrical integrity remains uncompromised.
The Future of Automotive PCBs
As the automotive industry moves toward electrification, autonomous driving, and enhanced connectivity, the role of PCBs will continue to grow. Future innovations in PCB technology will focus on:
High-Density Interconnect (HDI) PCBs: These PCBs allow for more components to be packed into a smaller area, which is crucial for the increasing complexity of automotive electronics, particularly in autonomous vehicles.
Flexible and Stretchable PCBs: As interiors become more customizable and user-focused, the demand for flexible and even stretchable PCBs will rise. These will enable more advanced, ergonomic designs in displays, sensors, and control systems.
Integration with 5G Technology: With the advent of connected vehicles and smart cities, 5G-enabled PCBs will become crucial for managing high-speed data transmission in real time.
Energy Efficiency: As EVs become more prevalent, PCBs will need to manage power more efficiently, not just for the vehicle’s operation but also to optimize battery life and range.
PCBs are the backbone of the automotive electronics revolution, enabling everything from basic controls to cutting-edge autonomous driving technologies. With the rise of electric vehicles and smart cars, the demand for high-performance, durable, and efficient PCBs is only set to increase. As a result, automotive engineers and PCB designers must collaborate closely to ensure that the next generation of vehicles is smarter, safer, and more efficient than ever before.
At iJbridge Incorporation, we recognize the crucial role PCBs play in the evolution of automotive technology. With our expertise in automotive design and embedded systems, we are committed to delivering innovative solutions that meet the challenges of the future. For more information about our services, visit us at www.ijbridge.com.